QUALITY CONTROL AND ASSURANCE
We make an extraordinary effort to ensure that the quality of every product you procure from UNIMA supply chain is flawless. While following the quality documents and certifications of standard machine elements with the most stringent procedure, we keep the traceability and quality control documents of the entire process starting from the raw material to the final product with immutable records for your special production needs and perform the strictest inspection possible against all possible problems that may be encountered in the future. We complete the necessary approval process by presenting the quality reports prepared specifically for the serial or lot numbers of all supplied products to our customers upon product delivery.
Apart from this, we regularly inspect the entire quality control processes and production flow, and we continuously inspect both our standard product suppliers and the factories and subcontractors we use for special production. Since our goal is to make the highest quality most accessible, the continuous inspections of our quality assurance system are inspected on the spot by independent and accredited 3rd party inspection companies.
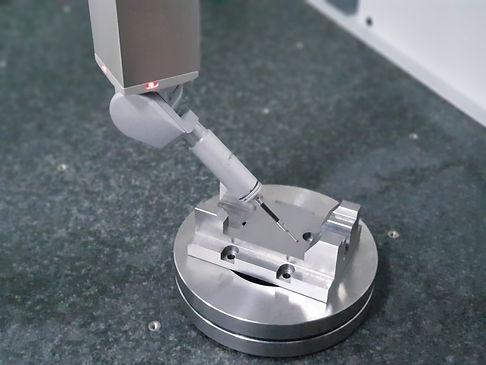
MEASUREMENT AND REPORTING
We perform the highest precision measurements with our CMM (3D measurement) devices, which are accepted worldwide and have the highest measurement precision, and share them with our customers as unchangeable records. We put all our special productions through standard measurement and quality control processes. It is one of our unchangeable rules that all productions, including our subcontractors, are checked and reported by our own quality team. In addition, all our equipment, including our extreme devices such as surface roughness, hardness and chemical analysis, undergo periodic calibration processes and their accuracy is constantly inspected. In addition, while some of the DT and NDT tests can be performed in our laboratory, we work with external sources for some of them. In this way, we can perform all detailed inspections and reporting.
QUALITY ASSURANCE
In addition to audits conducted by independent and accredited third-party organizations, we also conduct our own internal audits periodically and measure the efficiency of our quality system at certain intervals. We conduct all nonconformity, near-miss and preventive action activities in our company with the participation of all our personnel. In this way, we provide a higher quality and safer production process. In addition to systematic audits, we constantly inform our personnel and subcontractors in our supply chain with up-to-date information through planned and unplanned trainings and follow the benefit analyses of these trainings.


CERTIFICATES
We make every effort to fully and completely maintain all our work and established quality management systems. In order to maintain all of our quality assurance certificates that we have earned, we conduct the audits of our quality systems together with all our stakeholders, including our customers. The most important success that can be achieved for us is that we can successfully pass many customer audits at home and abroad and keep this system sustainable.